OSH and Work System Design
Health and Safety. Occupational safety and health (OSH) in general refers to all aspects of health and safety in the workplace. OSH often has a strong focus on primary prevention of hazards, as introduced by the World Health Organisation (WHO). Details of the scope of OSH is documented in national OSH legislation and may vary across countries. However, there are also similarities across countries, contexts and companies.
- Employers are responsible for safety and health of employees,
- employees are responsible for following safety and health rules and procedures, and
- both are asked to cooperate and engage in improvements.
- In several companies, OSH management is established to foster OSH at work by systematically analysing, assessing and designing tasks and working conditions according to OSH requirements and regulations.
- In practical terms basic OSH requirements include risk assessment procedures referring to different tasks or activities and working conditions as well as products or services.
Health is described, according to WHO principles, as a state of complete physical, mental and social well-being and not merely the absence of disease or infirmity. Promoting workers health is prevention of disease and combating risks. Measures are conductive, when optimising physical and mental activity at work through work system design, promoting more healthy diets, and protecting cognitive and emotional well-being at work. Health risk assessment should take severity of the effects into account; short-term and long-term as well as for people directly or indirectly involved. Relevant risks are those that can basically be identified, significant risks are those that factually lead to impairment, injury or disease.
Safety has variations in meaning occurring across contexts. A traditional view describes safety as freedom from unacceptable risk, i.e. referring to a negative connotation of types and frequencies of accidents, incidents and damage. Views with a positive connotation strive for safety as an ability to succeed, establish, maintain and improve safety in terms of successes under varying conditions. The latter perspective changes understanding, analysis, design and evaluation of the safety performance of organisations as well as values efforts to establish safety controls and design requirements in human factors and ergonomics (HF&E) to improve OSH at work.
Hierarchy of controls. Measures to improve health and safety of employees at work usually cover prevention of occupational accidents, occupational diseases and work-related health risks as well as human tasks and working conditions according to HF&E design requirements. Despite differences in legal OSH regulations across countries, the hierarchy of controls remains similar across countries and application contexts. It guides selection of effective measures for prevention and risk reduction in work system design, following levels according to a "STOP!" principle (see Figure 1).
Measures that eliminate and substitute risks are preferred over technical preventive measures for risk reduction. The latter are considered more powerful for risk reduction than organisational measures since they intervene directly at the hazard and not indirectly in terms of how to organise activities with regard to hazards. OSH interventions along levels lower in hierarchy are assumed to be less effective, albeit sometimes required and/or often used as supplemental measure. The hierarchy of controls is at the centre of the Prevention through Design (PtD) concept directing preventive measures for risk reduction to become effective early in the design of work tasks, working conditions, products, and services. Explanations for controls of the STOP! hierarchy with example measures are given below.
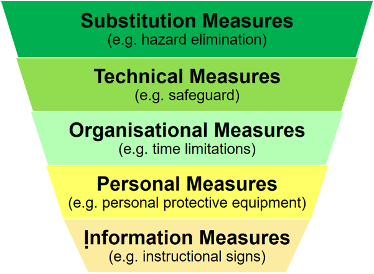
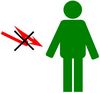
Substitution control and measures
In the present context, substitution measures cover those that eliminate or totally remove hazards and those that substitute or replace hazards. As a result, the worker in specific interaction should face zero risk or at least a lower risk. Examples from the perspectives of Human Factors, Ergonomics and Safe Machines are as follows
- Lubrication service points should be designed for ergonomic reach and away from moving parts of a machine.
- The use of special low noise circular saws will reduce the level of noise during human-system interaction; instead of using standard high noise circular saws.
- Manufacturing should be designed that truck motors are lowered into caverns to allow workers for assembly at ground level instead of working at height on scaffolding.
- Water-based paint should be used whenever possible and application of lead-based paint should be avoided.
- High quality elements in product design such as larger fans should be used for running smoothly at low noise instead of noisy high-pitched smaller fans.
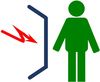
Technical control and measures
Technical or engineering measures reduce risks often by isolating the hazard from the workers. While in this case hazards stay or hazardous parts remain, work system design, integrated safeguards or similar add-ons shield or separate hazards safely from workers. In general, technical measures can address most components of work systems ranging from the work task, place, equipment, and environment. Sometimes, technical measures may seem more cost-intensive at the outset compared to other measures lower in the hierarchy. Due to safe and healthy working conditions and less complicated procedures at work for all employees, technical measures also reduce future costs and in the long run, if not already less expensive right from the beginning. Examples from the perspectives of Human Factors, Ergonomics and Safe Machines are as follows
- Some basic principles of these measures refer to process control, i.e. intervening technically in how to reduce the risk such as steam cleaning instead of solvent degreasing, to enclose or isolate hazards such as remote instead of direct control, to ventilate such as installing hoods that capture hazardous substances in the air.
- Technical measures are use of mobile elevating work platforms rather than scaffolding rather than work platform rather than ladders rather than fall arrest equipment for working at different levels of height.
- Instead of physical barriers between employees and hazards such as enclosures and isolation, remotely controlled equipment does serve as technical preventive measures.
- Accumulator power supply or wireless data connections should be used as technical measures to prevent from tripping hazards while using wired connections at work or when using head-mounted displays in virtual scenarios.
- In kitchens, fume hoods as technical measures can remove airborne contaminants. Similar, in food industry often transparent polycarbonate guards are used instead of grid guards to prevent from food particle splashing during operation.
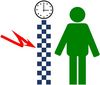
Organisational control and measures.
Changes in work organisation or procedures for ways of task performance are part of organisational preventive measures; sometimes also referred to as administrative controls. Organisational measures do not remove hazards, but limit or prevent hazard exposure of employees in space and time, i.e. through application of threshold limit values (TLV) for exposure per shift without adverse effects. Examples from the perspectives of Human Factors, Ergonomics and Safe Machines are as follows
- Application of threshold limit values (TLV) for exposure per shift without adverse effects could be an organisational limitation for hazard exposure of employees in space and time.
- Examples also include changes in work procedures and work processes, i.e. locking-out tagging-out (LOTO) procedures for repair and maintenance of machinery, completion of installations at night when fewer people are at work as well as safe work procedures and instructions for error correction of a milling-machine. Other examples for organisational controls comprise establishing of safety management systems and introducing emergency procedures in case of fire, release, spill, or injury. Additional examples are working time arrangements such as job-rotation schedules that limit the amount of time an individual worker exposed to hazardous working conditions, and the application of work-rest schedules that limit the length of time a worker is exposure to a hazard.
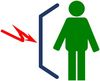
Personal control and measures
Personnel training and personal protective equipment (PPE) belong to well-known personal preventive measures. For personal measures it is desirable that it is designed for individual use and is tailored for individual training needs. These measures provide a barrier, cover, envelope, or shell around the individual employee that should improve and provide some resistance against hazardous impacts around. Examples from the perspectives of Human Factors, Ergonomics and Safe Machines are as follows
- Into this category belong all types of training and coaching as well as safety clothing such as smart textiles, safety overalls, suits, helmets, glasses, gloves, footwear including shoes, and hand, arm, face, hearing and respiratory protection.
- PPE always needs to be instructed and adjusted to individual requirements according to human factors and ergonomics, e.g. fall arrest equipment, and sometimes examinations are required before recommendations can be given whether or what kind of PPE would be suitable (e.g. respirators, diving gear).
- Personal measures are assumed among the least effective due to addressing individuals only, the potential for damage to render PPE ineffective or for distraction that may mislead trained behaviour and its potential to replace existing hazards by others (e.g. use of gloves at machines with feed in or rotations).
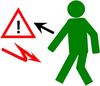
Informational control and measures
Hazards will not be removed by informational prevention measures. But they intend to inform the employee about potential hazards and assume that information will reach the receiver, is properly understood and implemented into behavioural activities. Sometimes information refers to the hazard itself and includes instructions about how to behave and what actions to take as well as address potential consequences. These measures are the least effective ones, because it is not even guaranteed that information will reach the addressee. Therefore, informational measures should be treated as additional support in risk control and should never be the only one. Examples from the perspectives of Human Factors, Ergonomics and Safe Machines are as follows
- Examples range from installation of signs and warning labels over work procedure instructions up to instructional information.
References:
- Lehto, M.R. & Cook, B.T. (2012). Occupational Health and Safety Management. In: G. Salvendy, G. (ed.), Handbook of Human Factors and Ergonomics (701-733). Hoboken: Wiley.
- EN 614-1. Safety of machinery - Ergonomic design principles - Part 1: Terminology and general principles.
- EN ISO 12100. Safety of machinery – General principles for design – Risk assessment and risk reduction.
- Hollnagel, E. (2014). Safety-I and Safety-II: The Past and Future of Safety Management. Farnham: Ashgate.
- Radandt, S., Rantanen, J. & Renn, O. (2008). Governance of Occupational Safety and Health and Environmental Risks. In: H.-J. Bischoff (ed.), Risks in Modern Society (127-258). Heidelberg: Springer Science+Business Media.
- WHO (2020). Basic documents (49th ed., including amendments adopted up to 31/03/2019). Geneva: World Health Organisation (WHO).